Inductive sensors zeroing in on electric motors
Olivier Brunel, E-Mobility & Strategic Development Market Manager, explains how inductive sensors are gaining ground in the electric motor market. To prove it, the contract signed with Volkswagen in 2018 is scaling up rapidly!
EFI Automotive develops accurate, lightweight, energy-saving and easy-to-integrate position sensors for hybrid and electric vehicles. Based on inductive technology, they are starting to make inroads into the market share held by the resolver, which has up until now been the benchmark. The first contract was signed in 2018 with VW, followed by others in China and Europe.
The position sensor plays a key role in electric motors: it locates the rotor magnets and is therefore able to finely adjust the stator magnetic field. The more accurate it is, the greater the efficiency and the more a vehicle can cover the miles without losing battery charge. “It is difficult to ignore,” notes Olivier Brunel, E-mobility & Strategic Development Market Manager. “Of course, there are also position controls that use algorithms, and so not position sensors, for example in fans. But these are not accurate enough for the automotive industry, which aims to maximize drivetrain efficiency improvements.”
EFI Automotive: conducting inductive sensor R&D since 2011
Today, the position sensor market is dominated by resolver technology, a type of rotary transformer that measures the angular position of the shaft. Although its precision is highly regarded, it suffers from one drawback: it has to cover the whole area of the rotor, due to its ring shape, and must be fitted very close to the motor. If there is a failure, it all needs to be dismantled!
In 2011, these limitations led EFI Automotive to launch an inductive sensor R&D program. “It was a gamble: it is always hard to move away from an established solution. But we knew that this technology had its advantages. It is more compact, is suitable for all motors and can be fitted away from the motor, which facilitates maintenance. This selling point was very important to VW, our biggest client.”
The main components of an inductive sensor are its coils. Having picked up a high-frequency current, a transmitter coil emits a variable magnetic field right through the coil. Any nearby metallic object therefore takes on the induced current and in return, emits a magnetic field, which is picked up by the receiver coils. This reaction is proportional to the sensor-object distance; the position of the aforementioned object is deduced from this.
Excellent operating reliability
The inductive sensor is smaller than the resolver: for VW, it is semicircular. It consumes around six times less energy. It can withstand electromagnetic disturbances, which are very strong in an electric motor whose coils receive a frequency of several kHz. It measures the shaft position to within 0.3%, despite it starting at 20,000 revolutions per minute.
It delivers excellent operating reliability: EFI Automotive products comply with ASIL D as defined by the ISO 26262 standard. “The manufacturers are so sensitive to this area that some of them even provide a second sensor in addition to the first,” notes Olivier Brunel.
However, it is when it comes to integration flexibility that the inductive sensor really makes a difference. Remember that an electric motor is a very confined space. Moreover, the ring shape of the resolver offers no flexibility, whereas the inductive sensor is smaller and can be installed at the end of the shaft, or fitted in a notch in the motor casing that can be accessed externally. “We are developing a customized solution for each vehicle and each type of motor. It includes the sensor itself and its mounting feet. Everything is done to limit the footprint.”
Hybrid vehicles and the inductive sensor: reduced costs compared to the resolver
This flexibility is highly valued in hybrid vehicles, in which the electric motor, installed close to the internal combustion drivetrain, has a large diameter. The resolver, which must cover the whole circumference, is inevitably large and expensive. The significantly more compact inductive sensor works much better.
However, currently, the resolver continues to dominate the position sensor market. This is primarily because its electronic power system and its data processing algorithms have been understood for a long time and are immediately available, whereas moving to inductive sensors means starting from scratch.
Moving toward inductive sensors with a digital sensor
EFI Automotive has reason to believe in inductive sensors: the contract signed with VW in 2018 has since increased in volume, with hybrid vehicles booming, and several other contracts have been concluded in China and in Europe. These contracts will lead to mass production between 2021 and 2023.
There is also going to be a significant evolution: the communication protocol for sensors will move from analog to digital. This will mean less electric wiring and direct access to the angular position, instead of post-processing of the received signal (sine and cosine). In addition, exit signals could be analyzed to detect failures, faults and drift. It is thought that the digital inductive sensor will therefore offer an additional level of reliability.
“The market is preparing for this evolution but is also struggling with an unknown quantity: which digital protocol will assert itself and become the standard?” explains Olivier Brunel. “We have chosen to move forward without waiting, with partners who produce digital chips. By the end of 2021, we could have products to sample and to make available to our clients.”
Olivier Brunel
E-MOBILITY & STRATEGIC DEVELOPMENT MARKET MANAGER
It is always hard to move away from an established solution. But we knew that this technology had its advantages. It is more compact, is suitable for all motors and can be fitted away from the motor, which facilitates maintenance.
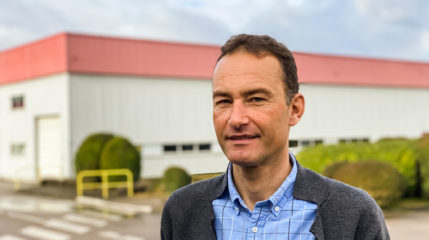