SAFETY: EFI AUTOMOTIVE, EXPERT IN OPERATIONAL SAFETY
Stéphanie Daussin is in charge of Functional Security, of the Management of the Reference System at system level and of the implementation of training in the group. She enlightens us on the implementation of product safety. This mainly concerns the functional safety of electrical and/or electronic products in the automotive industry, but not only. For her and EFI Automotive, safety is everyone’s business!
Beyond a commercial issue, product safety is above all a public health issue and the automotive industry is no exception to this rule. This is why the implementation of functional safety requirements makes the development and production of systems that have an impact on vehicle safety more reliable. It is for these purposes that the ISO26262 standard was created in 2011 and that a specific chapter was added to the automotive quality management standard, IATF16949 version 2016. It is therefore only natural that functional safety management has become a strategic issue for EFI Automotive.
The ISO26262 standard on functional safety, which has always applied to the electrical and/or electronic systems of vehicles under 3.5T, evolved at the end of 2018 to extend its scope to all motor vehicles. As a result, buses, trucks, and motorcycles are now included in its scope. But beyond this standard, functional safety management is also based on the application of quality management requirements (IATF16949) and in particular for functions or systems not covered by ISO26262. This is why, with or without ISO26262 requirements, our sensors contribute to making vehicles safer.
ZERO RISK DOES NOT EXIST, BUT THE APPLICATION OF NORMATIVE REQUIREMENTS MUST MAKE IT “ACCEPTABLE”.
By definition, zero risk does not exist. On the other hand, thanks to a structured approach that applies to all levels of the company, to the respect of standards (design, development, production, quality management) and of the state of the art, manufacturers are obliged to minimise this risk in order to make it tend towards a value that remains “acceptable” for users. This is why the application of strict rules, proven methods and analyses is fundamental. “By analyzing the product’s life cycle, by the choice of concepts, materials and the different diagnostic methods that are implemented at the system level, we ensure that these risks are limited,” explains Stéphanie. A failure that is detected is a failure whose effect can be reduced if it cannot be eliminated. For example, a system can send a warning message to the driver to avoid an accident with potentially more serious consequences. This is the principle of reversing radars: they indicate by an audible signal that one is approaching the risk zone before the danger is effective. The implementation of these protocols or devices is then the subject of collaborative work between equipment manufacturers and constructors.
Not all safety systems have the same level of risk. In fact, in ISO26262, we are going to analyze the life situations of a vehicle and identify their effects in order to evaluate them according to three criteria (severity, probability of exposure and controllability). The result of this combination then allows us to associate to each safety objective its level of risk (ASIL level) and consequently the number of normative requirements to be respected as well as the level of reliability required for the product. We will then adapt the response scale according to the risk.
For EFI Automotive, there are various products available today that have to meet these new requirements. From crankshaft speed sensors, brake pedal position sensors to inductive position sensors for electric motors, they are all already in production. But far from resting on its laurels, the company is diversifying by developing new mechatronic products that will tomorrow integrate hardware and software for systems such as intelligent actuators. “Customer or supplier, security is everybody’s business” says Stéphanie!
THE INCREASING SHARE OF ELECTRONICS DOES NOT AFFECT VEHICLE RELIABILITY
The integration of more and more electronic systems in vehicles helps to improve their safety, comfort or performance. At the beginning of the 2000s, the increase in the number of these systems and the implementation of new technologies led to an increase in the number of failures related to electronics.
Today, however, the evolution of our knowledge, the application of the state of the art and the creation and implementation of new standards such as ISO26262 make it possible to improve the reliability of vehicles.
EFI Automotive, through its presence on the automotive market with car manufacturers and system integrators, therefore contributes with its technical solutions and expertise to making vehicles more reliable.
ZERO RISK DOES NOT EXIST, BUT THE APPLICATION OF NORMATIVE REQUIREMENTS MUST MAKE IT “ACCEPTABLE”.
By definition, zero risk does not exist. On the other hand, thanks to a structured approach that applies to all levels of the company, to the respect of standards (design, development, production, quality management) and of the state of the art, manufacturers are obliged to minimise this risk in order to make it tend towards a value that remains “acceptable” for users. This is why the application of strict rules, proven methods and analyses is fundamental. “By analyzing the product’s life cycle, by the choice of concepts, materials and the different diagnostic methods that are implemented at the system level, we ensure that these risks are limited,” explains Stéphanie. A failure that is detected is a failure whose effect can be reduced if it cannot be eliminated. For example, a system can send a warning message to the driver to avoid an accident with potentially more serious consequences. This is the principle of reversing radars: they indicate by an audible signal that one is approaching the risk zone before the danger is effective. The implementation of these protocols or devices is then the subject of collaborative work between equipment manufacturers and constructors.
Not all safety systems have the same level of risk. In fact, in ISO26262, we are going to analyze the life situations of a vehicle and identify their effects in order to evaluate them according to three criteria (severity, probability of exposure and controllability). The result of this combination then allows us to associate to each safety objective its level of risk (ASIL level) and consequently the number of normative requirements to be respected as well as the level of reliability required for the product. We will then adapt the response scale according to the risk.
For EFI Automotive, there are various products available today that have to meet these new requirements. From crankshaft speed sensors, brake pedal position sensors to inductive position sensors for electric motors, they are all already in production. But far from resting on its laurels, the company is diversifying by developing new mechatronic products that will tomorrow integrate hardware and software for systems such as intelligent actuators. “Customer or supplier, security is everybody’s business” says Stéphanie!
THE INCREASING SHARE OF ELECTRONICS DOES NOT AFFECT VEHICLE RELIABILITY
The integration of more and more electronic systems in vehicles helps to improve their safety, comfort or performance. At the beginning of the 2000s, the increase in the number of these systems and the implementation of new technologies led to an increase in the number of failures related to electronics.
Today, however, the evolution of our knowledge, the application of the state of the art and the creation and implementation of new standards such as ISO26262 make it possible to improve the reliability of vehicles.
EFI Automotive, through its presence on the automotive market with car manufacturers and system integrators, therefore contributes with its technical solutions and expertise to making vehicles more reliable.
A NEW STANDARD BEING DEVELOPED FOR AUTONOMOUS VEHICLES
The ISO26262 standard now focuses on the functional failures of electrical and/or electronic systems, but with the arrival of autonomous vehicles and the new constraints attached to them, new design, verification and validation rules are emerging.
The appearance of new functions such as emergency braking systems and advanced driver assistance systems (ADAS) lead to risk analyses linked to the inadequacy of the functions provided or misuse by people (reasonably foreseeable risk). This is why these new requirements will now be dealt with in a new reference frame ISO21448: Road vehicles – Safety Of The Intended Functionality (SOTIF).
Stéphanie Daussin
GROUP QUALITY LEADER, SAFETY SPECIALIST
Zero risk does not exist, but the application of normative requirements must make it “acceptable”.
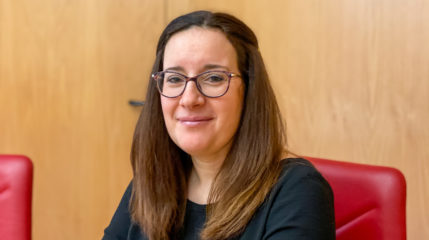